Tesla CEO Elon Musk has once again shocked the automotive world with a claim that seems to defy physics: the upcoming Cybercab production line will churn out one vehicle every 5 seconds. Ambitious targetârevealed during all-hands meetingâwould represent a manufacturing breakthrough so significant that even veteran automotive engineers are struggling to comprehend how it could be possible.
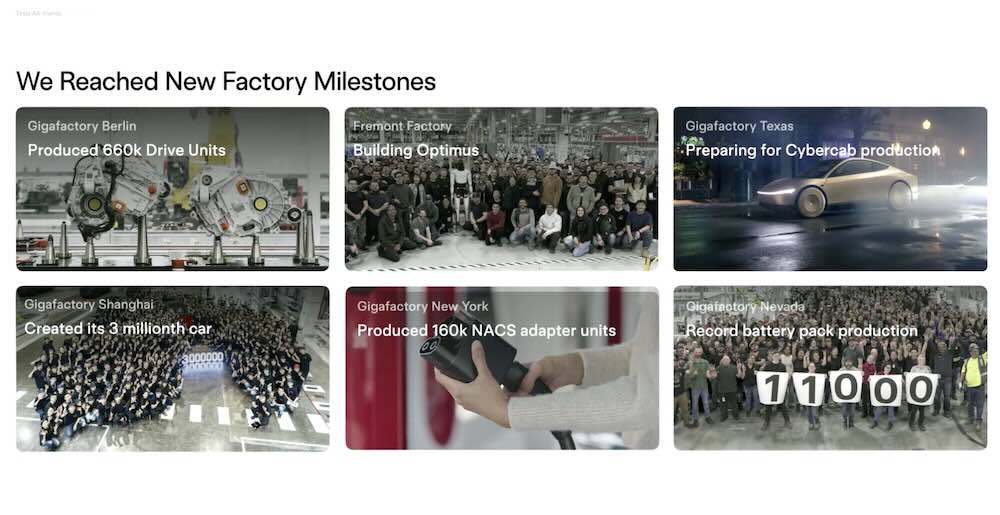
Tesla all-hands livestream
To put this in perspective, Tesla’s current crown jewelâthe Model Y production lineâdelivers a vehicle every 35 seconds, already considered best-in-class within the global automotive industry. Traditional automakers typically operate at much slower rates: Toyota’s TNGA platform runs at around 60 seconds per vehicle, Volkswagen’s MEB platform at 65 seconds, and Ford’s impressive F150 line at 53 seconds.
Most industry experts have long considered 40 seconds per vehicle to be the absolute floor for mass production. Anything faster would theoretically require prohibitively expensive equipment and result in unsustainable cost-to-output ratios.
So how exactly does Tesla plan to achieve what amounts to a sevenfold improvement over conventional manufacturing wisdom?
The answer lies not in incremental improvements to existing processes, but in a fundamental reimagining of both the product itself and how it’s built.
According to statements from Tesla’s VP of Vehicle Engineering Lars Moravy and insights from CyberCab’s Chief Engineer Eric Eklund, Tesla is implementing what they’re calling an âunboxed processâ revolutionary manufacturing approach that’s already being installed at Giga Texas, with prototype builds expected this summer.
“We have a big rear casting, a big front casting. We have two hot stamped door rings that will be laser welded together,” Lars explained. “The castings aren’t even gonna be painted on this. We’ve done work with our materials team, we got corrosion under control. Only area you are going to see some paint is the hot stamped door rings.”
This radical departure from traditional automotive assembly involves four key innovations:
While the Model Y uses 61% self-developed electronic and electrical components, CyberCab will utilize 100% in-house parts. Higher integration significantly simplifies assembly by reducing the number of separate components that need to be brought together.
The structural architecture shows similar improvements. The updated Model Y uses die-casting only for the rear portion of the vehicle, resulting in approximately 200 structural components. The CyberCab, however, employs die-casting for both front and rear sections, reducing the structural component count to around 80âa 60% reduction that dramatically streamlines assembly.
Traditional automotive manufacturing devotes enormous resources to painting operations, which include not just the application of color but also extensive drying, curing, and quality control processes. Tesla has effectively eliminated this entire stage for the CyberCab.
The company’s materials team has developed corrosion-resistant die-cast aluminum parts that don’t require protective painting. Additionally, exterior panels are made from injection-molded polyurethane with color integrated directly during the molding process. Simultaneous coloring and molding yields panels with fully embedded color, eliminating the need for separate painting operations.
As a result, the CyberCab production line won’t include a dedicated painting shopâa first in modern automotive manufacturing.
The CyberCab was designed from the ground up as a dedicated robotaxi, not as a conventional passenger vehicle later adapted for autonomous operation. Focused approach allows Tesla to eliminate numerous components that would be essential in a human-operated vehicle.
Gone are interior and exterior rearview mirrors, steering wheel, pedal assembly, steering columns, linkages, and associated wiring. An entire row of seats has been removed as well. Vehicle also features just two doors instead of the standard four, further reducing assembly complexity.
These simplifications create cascading efficiencies throughout the manufacturing process, removing dozens of assembly steps that would otherwise be required.
Perhaps the most transformative aspect of the CyberCab production system is Tesla’s shift from sequential to parallel assembly. Rather than a linear, sequential production line, Tesla is embracing a modular architecture that enables parallel manufacturing of vehicle sections.
In traditional automotive manufacturing, vehicles move along the assembly line in a linear fashion, with components added one station at a time. CyberCab’s “unboxed” approach splits the vehicle body into four sections that are assembled simultaneously:
- front die-cast structure
- structural battery chassis combined with seats
- rear die-cast part (with fewer components due to removed seating)
- left and right door frames
Only after these four major subsystems are independently assembled do they come together for final integration. Parallel processing enables dramatically faster overall production rates without requiring each individual station to work at impossible speeds.
Tesla’s journey to this manufacturing breakthrough can be traced through its continuous refinement of the Giga Shanghai facility. Initially producing vehicles at a 45-second cycleâconsidered excellent by industry standardsâShanghai improved to 40 seconds by 2023 through production line optimizations. 35-second cycle time for Model Y production is widely believed to have originated at this facility.
These incremental improvements provided critical insights that informed the CyberCab’s revolutionary manufacturing approach. But the scale of the leap from 35 seconds to 5 seconds suggests that Tesla isn’t merely optimizing existing processesâit’s completely reinventing them.
If Tesla succeeds in implementing this 5-second production cycle, the implications for global manufacturing extend far beyond the automotive sector. A single CyberCab production line would deliver output equivalent to five Giga Shanghai factories combinedâa facility that currently produces 1.1 million vehicles annually.
This unprecedented production velocity would challenge fundamental assumptions about the relationship between manufacturing speed, quality, and costâassumptions that have governed industrial production since the early days of Henry Ford’s assembly line.
More immediately, it would give Tesla an extraordinary competitive advantage in the emerging robotaxi market. While competitors struggle with the economics of producing autonomous vehicles at scale, Tesla would be able to flood target markets with CyberCabs at a pace that would make meaningful competition nearly impossible.
Despite the detailed technical explanations provided by Tesla executives, significant questions remain about how the 5-second target will be achieved in practice.
The “one car every 5 seconds” claim presumably refers solely to the final assembly stageânot to a scenario where raw materials are transformed into a complete vehicle within that timeframe. Even with the revolutionary “unboxed process,” physics of moving physical components into position and securing them properly would seem to impose hard limits on assembly speed.
Additionally, quality control processes typically introduce constraints on production velocity. Tesla has frequently faced criticism regarding build quality, and dramatically increasing production speed could potentially exacerbate these concerns without corresponding innovations in quality assurance.
Production equipment for the CyberCab is reportedly already being installed at Giga Texas, with the first prototype builds expected this summer. Aggressive timeline suggests Tesla is confident in its manufacturing breakthrough and eager to begin proving its viability.
If successful, CyberCab production system wouldn’t just represent an incremental improvement in automotive manufacturingâit would constitute a paradigm shift comparable to Ford’s original moving assembly line or Toyota’s just-in-time production system.
The ability to produce vehicles at this rate would fundamentally alter the economics of autonomous mobility, potentially enabling Tesla to deploy Robotaxi fleets at a scale and price point that would make personal vehicle ownership increasingly unnecessary for many urban residents.
More broadly, it would cement Tesla’s reputation not just as an electric vehicle company or an autonomous driving pioneer, but as a manufacturing innovator whose production technologies might eventually prove more valuable than the products they create.
As with many of Elon’s ambitious claims, industry skepticism remains high. Yet Tesla has repeatedly achieved technical feats that critics initially dismissed as impossible. Whether the 5-second CyberCab production line joins that list of improbable successes or remains an aspirational target will likely become clear within the coming year.
Related Post
Tesla Robotaxi vs UBER: Former Executive Reveals Why CyberCab Will Transform Ride-Hailing
Tesla Rejects Uber Partnership, Sets Stage for Autonomous Ride-sharing Showdown in Austin
Tesla Secures First California Permit on Path to CyberCab Robotaxi Service | What It Means